Nine Tips for Disaster Preparedness
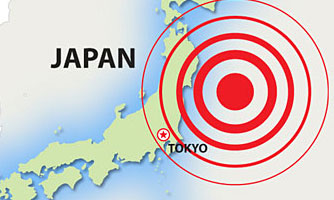
While it may be some time before the extent of the devastation in Japan - both in human life and economic impact - is fully determined, police have already confirmed over 11,004 deaths and 17,339 others who are missing, according to Japan's Kyodo news service. All told, the number of deaths estimated by the Japanese government may exceed 18,400.
Currently, concern is focused on fuel rods at three nuclear reactors at the Tokyo Electric Power Co.'s Fukushima Dai-ichi plant, which are believed to be in various stages of melting. Also, a container for spent fuel at a fourth reactor has been damaged and is leaking radioactivity. Japanese authorities have ordered the evacuation of a 19-mile radius around the plant while they work to restore power in hopes of bringing cooling systems back online. The U.S. has recommended that its citizens living within 50 miles of the plant evacuate the area or take shelter indoors. Approximately 180,868 people are staying in temporary shelters, while thousands of others are without power or clean water. Transportation and communications within the most affected areas is spotty.
Truly, disaster on this scale is something nobody wants to think about, but which organizations have to be prepared to deal with. Safety and security protocols for employees as well as company assets and business continuity are critical to plan for in advance and maintain, even to the extent of planning for the totally unexpected with scenarios that can utilize multiple flexible contingencies and guidelines.
There are also ripple effects from any event of this magnitude that require contingency planning. In the case of Japan, one factor has been the countries just-in-time supply chain , which in the wake of these disasters has begun affecting many businesses and trading partners in the region and around the globe. As radiation is now being found in some food and dairy products, any businesses sourcing farms in that area will also need to look to other options; and radiation traces are quickly being discovered around the globe. These concerns will likely expand as the extent of radiation contamination is continuously updated. Resources needed inside the worst hit areas will also impact supply chains for food, fuel and medicine that were previously directed elsewhere.
Harsh winter weather, hurricanes, earthquakes, tsunamis, terrorist threats and pandemic flus have all made headlines in recent years. Situations such as these, although unpleasant to contemplate, are all fodder for scenario planning. That is, organizations can develop scenarios around such issues and then draft up action plans - or at least a set of good ideas - to help them react more quickly when a real crisis emerges. This can help minimize disruption in case of emergencies.
In crafting possible tactics for dealing with crises, organizations should consider the following suggestions and principles:
- Have emergency plans in place, written down, regularly updated and ready to deploy. Make sure those plans are as flexible as possible so they can be effective in a variety of circumstances. Don't wait until disaster strikes to build the flexible infrastructure you'll need to implement your plans. These plans should have an owner who is a senior executive involved in strategic planning.
- Employee safety should always be the number-one priority. Whenever possible, cancel non-essential travel and have employees stay put until the crisis is over. Make travel decisions at the executive level, considering impact on business operations, the need for an on-site presence and the potential costs of rescheduling. Make special note of those with medical problems, as well as their required medical supplies and the availability of refills.
- Keep communications flowing. Communicate your company's back-up plans and policys regularly with employees and ensure that employees communicate their status regularly through predetermined channels. Maintain links to appropriate authorities and monitoring agencies. Include travel departments and travel vendors in the process where necessary. Redundant and secondary communication channels are recommended, such as multiple but coordinated call-in lines located in different regions and monitoring of web-based and emergency services channels.
- When appropriate, ask employees to make reasonable attempts to return to work in the aftermath of a crisis even as your company maintains flexibility and understanding of their circumstances. In some cases, contingent travel options may be equally inaccessible due to overburdening of those systems. Where applicable, having virtual work options and IT infrastructure that supports remote workers is optimal for maintaining productivity.
- Make the most of regional offices or business units and set up pre-determined gathering hubs where stranded employees can connect. Map out where employees are and in what numbers and confirm contact details.
- Alleviating worry and burden from a stranded or otherwise effected worker can positively impact short-term productivity, long-term engagement and morale levels. Absorbing costs and assuring security at home for those with child care and elder care responsibilities is a great comfort. Such over-and-above thinking in trying times will be appreciated and remembered.
- While absences due to natural disasters are generally excusable, companies are not necessarily required to pay for time away from work. Clearly communicate telecommuting, flex-scheduling, paid time and unpaid time options, being as understanding to extenuating circumstances as possible. In cases where employees are stranded while on vacation, ask if they would consider using paid time as opposed to unpaid leave. If it's possible to make up time or swap schedules, this may also be preferable. Make sure that options are consistently offered to avoid discrimination claims.
- Do not unreasonably burden workers who are able to report to work. In the event that staffing levels are seriously depleted for extended periods, scale workloads, adjust shift schedules and reset deadlines as needed to operate reasonably and sustainably.
- Just because there's no direct effect of the specific event doesn't mean your business won't be affected somewhere along the line. Services, suppliers, partners and customers are all factors to account for. Make them a part of your scenario planning process. Consider what echoes and ripples could resonate out from the present situation.
It shouldn't take a catastrophic event to initiate a review of disaster preparedness and plans shouldn't be gathering dust between reviews. It's better to work on and streamline these plans between emergencies and not during a crisis. Although the current situation in Japan, a country with exemplary disaster planning protocols, shows that no amount of forethought can trump natures unpredictable nature, every layer of protection put in place has cushioned the impact of this tragedy to some degree. Response to this disaster has truly been a case of mounting the best response possible to a tragedy of epic proportions.
For more, a comprehensive list of resources, services and information
- including EAP providers in Japan - is available from the Global Health Benefits Institute as a PDF document.
Please share your own disaster preparedness tips with other i4cp member companies. If your employees were affected by this tragedy, how has your organization responded and what plans did you have in place before hand?
Echoing the words of our friends at Osaka-based Takeda Pharmaceuticals: "We would like to express heartfelt condolences to the families of the victims, and we also sincerely wish the safety of the people affected by this earthquake and the earliest possible recovery of the relevant region."
Also, see how i4cp member companies are stepping up to aid Japan.
